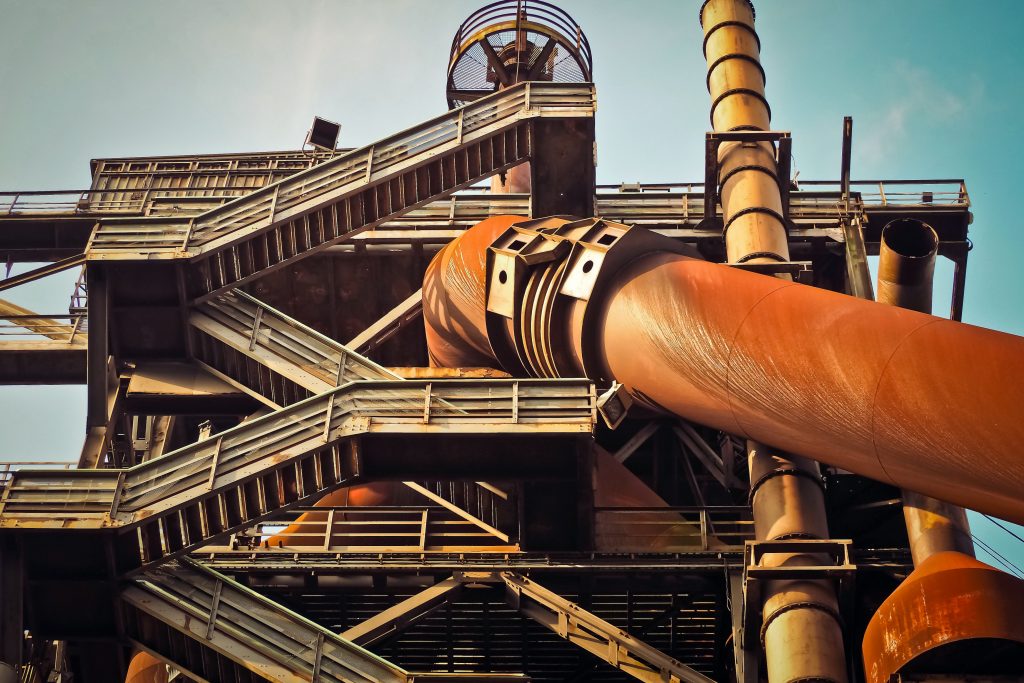
Pumps are integral components of any factory or industrial plant. If the pump experiences a downtime, there will be a costly and severe impact to the company’s bottom line. Some of the commonly used pumps are barrel pumps. They have a motor operated through electricity or air and a pump. These 2 units are universally interchangeable. Due to this feature, the Flux barrel pump can be operated effectively using different drive motors to suit the requirements of the operator. Factories and industrial plants rely heavily on the reliability of the machinery and equipment in their facilities. If the pump is not at optimal operation power, it will result in less output and costly repairs. As a result, you need to budget for pump maintenance to avoid such devastating consequences. Pump maintenance involves both corrective and preventive options. The corrective type of maintenance handles any pump failure issues that have already happened. It needs to be done very fast and efficiently to make sure the pump is working as required with no or less impact to the overall operation. However, you will have larger problems if you only rely on corrective maintenance options. Basically, this means that maintenance will only happen once the problem happens rather than preventing it from happening in the first place. To avoid any operational downtime caused by any unexpected issues with the pump, you need to introduce a preventative maintenance schedule. Here, you will plan for a periodic check of the performance of the whole pump. It also involves checking the parts of the pump that are prone to wearing out. Finally, don’t forget to check whether the joints and bearings have enough lubrication. By ensuring preventive maintenance is regularly undertaken, the maintenance will be handled before the problem happens thus preventing any downtime.
Employing a Periodic Pump Maintenance Schedule
Every day, you need to check the pump installation. Doing this allows you to trouble shoot and prevent pump breakdown. Here are some of the notable things to check.
- Corrosion
- Leaks
- Discoloration
- Evidence of rubbing or wear
- Overheating
- Clogging
- Unusual noises
On the other hand, there are some inspections that don’t need to be done regularly. In this case, preventive pump maintenance should be planned to fit into a periodic maintenance schedule. Here, there will be an outline of when certain tasks should be handle thus making maintenance a more efficient process. As a result, you will reduce the likelihood of any failures and downtime with your pump installation. It will also reduce the overall cost of ownership since replacing the worn out parts will be more affordable than repairing the entire pump. Here is an example of a schedule to follow.
Daily, 10 to 15 minutes
- Check for cavitation and bearing noise
- Check for bearing temperatures
- Check for motor current and voltage
Weekly, 20 to 30 minutes
- Check for vibration and noise
- Check for suction and discharge pressure
- Check for sealing leakage
Monthly, 20 to 30 minutes
- Check for coupling alignment
- Remove safety guards and check for shaft and auxiliary devices
- Add the lubrication oil if required
Annually, 2 To 3 Hours
- If it’s a spare pump run it and check for the capabilities
- Check for axial movement of motor shaft
- Remove all the auxiliary devices and clean them. These include the manometers, valves, sight glasses, piping etc.
- Remove all the coupling halves and check if there is any wear on the rubber part
- Renew it if necessary
2 Years, 6 To 8 Hours
- Remove the pump from the pimping and check the following parts then renew if necessary
- Wear plates/rings
- Impellers
- Shaft
- O-rings
Next, you should apply coating on un-machined surfaces. If you want the preventive maintenance to take place faster, you should keep spare parts for your pump on-site since you will reduce the downtime efficiently.